UPS Tracking UK
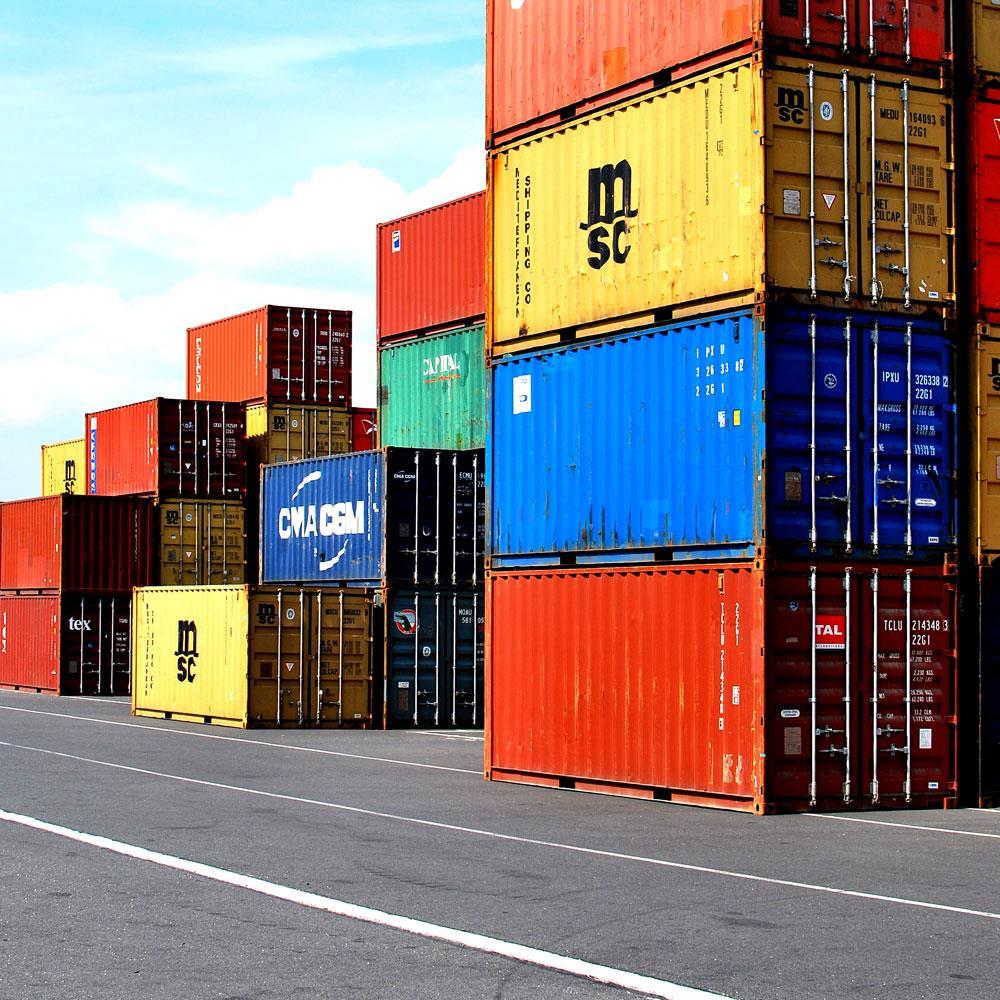
In logistics, there are various procedures, each of which can reach a high level of complexity. Information is also communicated and exchanged in every sub-steps or sub-processes, which is critical for the proper operation of the entire process chain. UPS Tracking UK While the specific logistical needs in each application area may change, the actual logistics procedures are quite similar.
Processes vary in complexity depending on the sector and organization, and some processes, such as urgent orders, are always a problem to plan and implement. The warehouse and its associated operations are critical components of a UPS Tracking UK company's logistics. Everything focuses on the most efficient use of space and the lowest possible running expenses, which are regularly evaluated using important data like inventory coverage. As a result, all logistical procedures must be closely connected and coordinated.
Because optimum coordination necessitates the utilization of know-how, time, money, and skilled labor, logistics operations rely on both external and internal knowledge. Despite the fact that logistics procedures are essentially similar, changing or optimizing them is always extremely personal, as the circumstances and specific requirements on-site vary greatly. The objective is to automate UPS Tracking UK as many logistical procedures as feasible. Goods delivery necessitates connection with the provider. The order confirmation and, if necessary, the shipment confirmation are the very minimum of this information exchange. This procedure may be automated to a large extent using an ERP system.
Track & Trace Your UPS Tracking Number
If the inventory arrives at the firm premises via truck, for example, traffic must be managed in terms of time and space by designating a certain location and a specific time frame for unloading. Following unloading, there is notification, inventory check, and recording in the company's inventory management system. The supplied inventory is subsequently assigned to a UPS Tracking UK storage location. If the merchandise was delivered in reusable containers, they must be booked, returned, or swapped as needed, with separate container management systems often in place.
Delivered products are carried to their storage site using industrial vehicles, for example, from the goods receiving area. Through forklift control systems or a higher-level control center, vehicle and worker movements in the warehouse are subject to logistical criteria in order to use all resources as efficiently as possible. Picking and picking of inventory occurs once items are required from the warehouse, and inventory is then delivered to the destination; this might be a manufacturing unit within the plant or shipment for distribution. Similarly, at this point of the operation, materials handling systems (material flow systems) can be integrated to automate the bulk of the transit route.
In order for needed materials to be delivered from the warehouse just-in-time, logistical supply to production usually follows set Kanban processes and also relies on complex implementations such as the Jidoka principle to trigger the replenishment process when replenishment is actually needed, not too early and especially not too late. Serial and batch numbers are also employed in manufacturing to guarantee that the origin, as well as the quality and finishing, can be tracked all the way from the factory to the end user. Production items can be packed there as well, but this is generally done during distribution.
Admin